IIoT and Mass Customization: How Do They Fit Together?
Mass customization can fulfill the needs of individual customers but can drive cost and complexity. We share how IIoT responds to those challenges as manufacturers shift to mass customization.
December 27, 2018
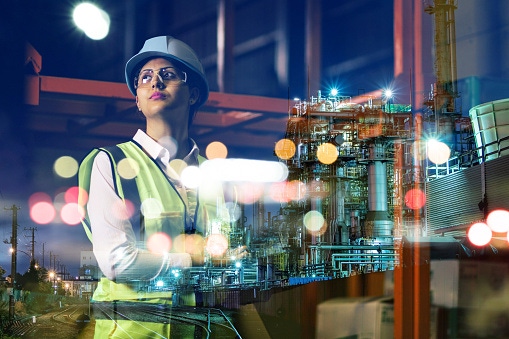
By Boris Shiklo
Recent Deloitte research shows that more than 50 percent of customers expressed interest in acquiring custom products. Empowered by the development of technologies, they are willing to become co-producers and have the opportunity to shape the products they purchase themselves.
To respond to the expectations of individual customers, enterprises have embraced mass customization, which allows them to create products tailored to the needs of a particular buyer while retaining high production volumes and relatively low production costs. As customers’ desires become increasingly diverse, however, mass customization can turn into mass confusion, adding complexity to manufacturing operations and creating excessive costs. Let’s see how IIoT can help.
The Role of Industrial IoT in Improving Mass Customization
IIoT boosts performance in the areas that are vital for mass customization, such as inventory, operations and supply chain management. By informing manufacturers of the precise status of every item at each segment of the production and supply chain, IIoT enables cost-effective mass production of customized products. Here’s what manufacturers achieve applying Industrial IoT solutions.
Optimal Inventory Levels
Imagine a dining chair manufacturer that offers customers the ability to “assemble” a chair they like from pre-manufactured parts. Customers can choose from ladder or Windsor backs, curved or straight legs, and striped or polka-dotted upholstery options.To ensure they have enough wood and fabric types for the production of any chair model, manufacturers could simply increase the inventory. Yet this approach adds costs, extends search times and complicates the manufacturing process.
With IoT, on the other hand, manufacturers can keep lower inventory levels, while still being able to meet the needs of the customers at the end of the supply chain. To enable that, individual inventory items receive RFID tags that contain encoded data, such as an item’s type, batch, serial number, etc. As tagged items go through the manufacturing process, RFID readers fetch the data from the tags and relay it to the cloud for processing (together with the data about the location of the corresponding reader and the time of the reading).
The cloud software aggregates and analyzes the data from multiple readers and provides manufacturers with real-time insights into the volumes and locations of materials and components, work-in-progress and finished goods. It allows an enterprise to balance the amount of on-hand inventory and, thus, lower inventory carrying costs and reduce lead times.
Agile Manufacturing Operations
To make small-batch production typical for mass customization profitable, the flexibility and agility of manufacturing operations are crucial.
For instance, a machining center assembles different shoe models. Every time it switches from assembling a pointy-nose shoe to an oval-nose shoe, a machine should be reset. Constant resetting significantly decreases machine use and results in fewer items being produced.
To pinpoint and avoid such interruptions, manufacturers turn to IoT development and implement technologies for monitoring machine use. Driven by the data fetched from equipment sensors, IoT-enabled solutions provide manufacturers with real-time information about key equipment utilization KPIs (TEEP, OEE, downtime, etc.), as well as identify a particular loss (such as setup and adjustment, reduced speed, etc.) behind the reduction in effectiveness.
With the real-time utilization data, manufacturers avoid potential breakdowns, bring idle time down to a minimum and gain greater agility.
A Flexible and Transparent Supply Chain
The flexibility and transparency of the supply chain is another parameter important for mass customization since customers demand realistic lead times and the possibility to track the location of the delivered products. At the same time, they are unwilling to be offered any products, the components for which are out of stock or still in transit.
Achieving it is quite difficult, especially when multiple parties are involved, including several tiers of suppliers, parts manufacturers, sub-assemblers, etc. With IoT, businesses get the opportunity to get greater visibility into the supply chain and improve it in such areas as:
Delivery of materials and components from suppliers.
Distribution of inventory across multiple echelons.
Delivery of finished products to the end customers.
With RFID tags attached to the packages, pallets, crates, containers, etc., manufacturers can monitor the location and condition of every individual package in transit and at a warehouse.
Moreover, analyzing historical data, manufacturers can reveal trends and make predictions to optimize deliveries, and say, choose optimal delivery routes and inventory storage models.
To Sum Up
Mass customization requires considerate inventory management, highly flexible manufacturing operations and a transparent supply chain. IIoT helps to increase efficiency at each stage. By fetching real-time data from sensors and/or RFID tags, IIoT allows businesses to produce customized products in an efficient way, sparing excessive costs and keeping operations smooth and aligned.
Boris Shiklo, chief technology officer at ScienceSoft, is responsible for the company’s long-term technological vision and innovation strategies. Under his supervision, the company’s development team has successfully fulfilled complex projects of more than 80,000 man-hours in Healthcare, Banking & Finance, Retail, Telecommunications, Public Sector and other domains.
You May Also Like